糖化鍋檢測:保障食品與生物工程安全的核心環節
糖化鍋作為食品工業、酒精生產及淀粉糖加工中的核心設備,承擔著淀粉液化、糖化反應的關鍵任務。其運行狀態直接影響產品質量、生產效率和能源消耗。糖化鍋檢測是確保設備高效、安全運行的核心手段,涵蓋材料性能、工藝參數、機械結構及安全防護等多維度內容。通過系統化的檢測,可有效預防設備故障、減少生產事故風險,并延長設備使用壽命。尤其在高濃度、高溫、高壓的工業場景下,糖化鍋的穩定性和耐腐蝕性直接關系到生產線的連續運轉能力。
糖化鍋檢測核心項目及技術要求
1. 溫度控制系統檢測
采用紅外熱像儀和數字溫度傳感器對加熱夾套、內膽溫度分布進行三維映射,要求溫度偏差值≤±1.5℃,重點檢測溫度梯度是否符合淀粉酶活性曲線要求。需驗證PID溫控算法響應速度,確保在物料濃度突變時能維持±0.5℃的動態穩定性。
2. 攪拌系統性能驗證
通過扭矩傳感器和激光轉速計測量攪拌軸功率消耗,要求單位體積功耗≤0.15kW/m3。使用PIV粒子成像測速技術分析流體剪切速率分布,驗證槳葉結構與轉速匹配度,確保糖化液粘度均勻性達到工藝標準(RSD≤3%)。
3. 密封性能與耐壓測試
采用氦質譜檢漏法檢測0.4MPa工作壓力下的密封性能,泄漏率應<1×10?? Pa·m3/s。通過液壓爆破試驗驗證設計壓力1.5倍下的結構完整性,同時檢測法蘭連接處的應力分布是否超出材料許用值。
4. 材質耐腐蝕性評估
使用電化學工作站測定316L不銹鋼在pH4.0-5.5糖化液中的點蝕電位,要求Eb>0.25V(SCE)。對焊縫區域進行晶間腐蝕敏感性試驗(ASTM A262 Practice E),確保在65℃酸性介質中無晶界腐蝕傾向。
5. 自動化控制系統校驗
對PLC/DCS系統進行冗余測試,驗證pH值、DO溶解氧等在線傳感器的測量精度(pH±0.05,DO±2%FS)。通過階躍響應試驗評估PID參數整定效果,要求物料濃度閉環控制的超調量<5%,調節時間<3T(T為系統時間常數)。
檢測周期與風險預警機制
依據TSG 21-2016《固定式壓力容器安全技術監察規程》,建議每12個月進行系統檢測,高頻使用工況需縮短至6個月。建立基于振動分析(VA)和潤滑油鐵譜分析的預測性維護體系,當齒輪箱振動速度值超過ISO10816-3標準的4.5mm/s或鐵譜磨粒濃度>500ppm時,觸發二級預警響應。

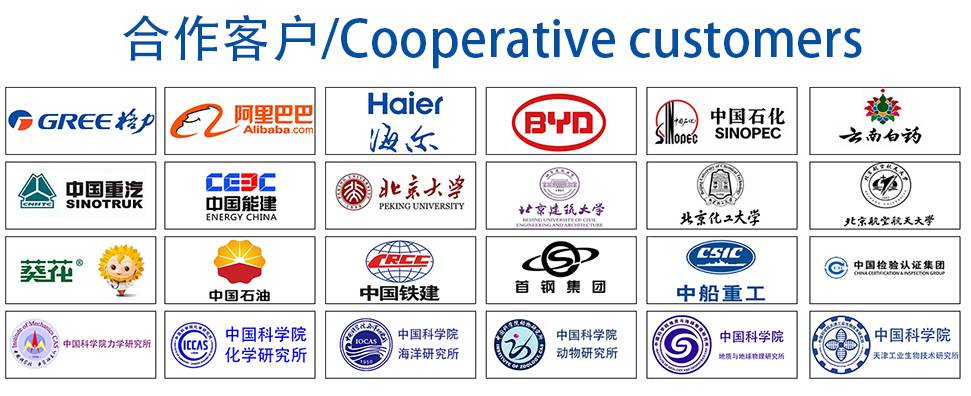