再制造內燃機檢測項目的核心內容與技術要求
再制造內燃機作為循環經濟與綠色制造的重要實踐方向,通過修復、升級或替換舊機部件實現資源高效利用,其性能與可靠性須達到甚至超過新機標準。在這一過程中,檢測環節是保障再制造產品質量的核心手段,涉及機械性能、材料特性、排放合規性等多維度指標。科學的檢測體系不僅能夠驗證再制造工藝的有效性,還能為企業降低返修成本、提升市場信任度提供技術支撐。
1. 基礎尺寸與幾何精度檢測
再制造內燃機的核心部件(如缸體、曲軸、凸輪軸等)需通過三坐標測量儀、激光掃描儀等設備進行幾何參數驗證,確保關鍵尺寸公差(如缸徑圓度、曲軸軸頸跳動量)符合原廠技術規范。對于存在磨損或變形的部件,需評估是否滿足再制造修復余量要求,避免因尺寸超差導致裝配失效。
2. 材料性能與表面狀態分析
采用顯微硬度計、金相顯微鏡對部件表面及基體進行檢測,重點監控關鍵運動副(如活塞環槽、氣門座圈)的硬化層深度和顯微組織狀態。同時通過磁粉探傷、超聲波探傷等技術排查裂紋、氣孔等缺陷,對于復合修復工藝(如激光熔覆、電弧噴涂)需額外檢測結合界面致密性。
3. 裝配質量與動態平衡測試
整機裝配過程中需執行扭矩校驗、間隙測量等工序控制,并使用動平衡機驗證曲軸組件的平衡精度(殘余不平衡量≤15g·mm)。渦輪增壓器轉子等高速旋轉部件需單獨進行超速試驗,確保在120%額定轉速下無異常振動或變形。
4. 臺架性能與排放合規性驗證
在標準試驗臺架上進行冷熱啟動、負荷特性曲線、耐久性等測試,功率輸出偏差應控制在±3%以內。排放檢測需滿足國六/歐Ⅵ標準,特別關注NOx(氮氧化物)與PM(顆粒物)的實時濃度。對于電控系統單元,還需通過OBD診斷接口驗證傳感器數據準確性與故障碼響應邏輯。
5. 密封性與耐久性專項檢測
采用氦質譜檢漏儀對燃油系統、冷卻系統進行密封性測試,泄露率需低于10-5 Pa·m3/s。模擬實際工況進行500小時強化試驗,監測機油消耗率(≤0.1%燃油消耗量)與氣缸壓縮壓力衰減幅度(周期降幅<5%)。
檢測標準的迭代與智能化升級
隨著再制造工藝的進步,檢測體系正逐步融合AI視覺識別、工業CT斷層掃描等新技術。通過建立數字化檢測數據庫,企業可實現歷史數據的趨勢分析與工藝優化,推動再制造內燃機檢測從單一合格判定向全生命周期質量管控轉型。

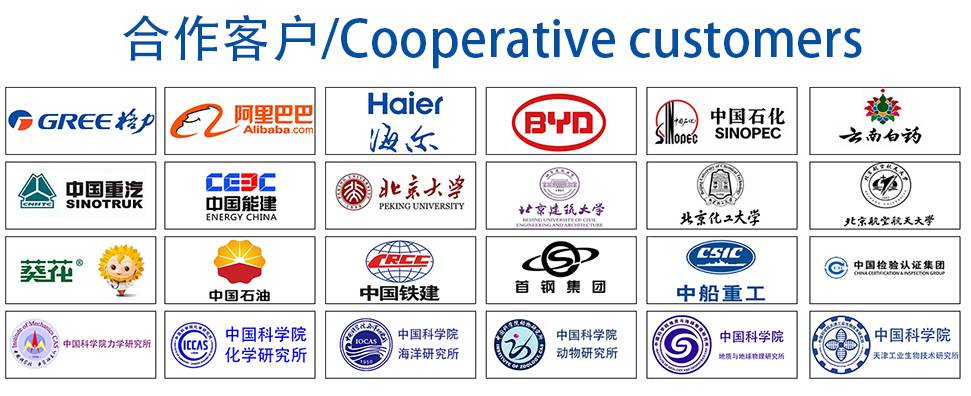