內燃機機油泵檢測的重要性及核心內容
作為內燃機潤滑系統的核心部件,機油泵承擔著向發動機各摩擦副輸送潤滑油的重要任務。其性能直接影響發動機的潤滑效率、散熱能力和使用壽命。據統計,約15%的發動機故障與機油泵異常直接相關。因此,機油泵檢測不僅是維修保養的重要環節,更是預防發動機重大損傷的關鍵措施。專業系統的檢測能夠有效發現泵體磨損、密封失效、壓力不足等問題,確保機油循環系統的高效穩定運行。
機油泵檢測核心項目
1. 泵體密封性檢測
通過壓力測試儀對泵體進行0.2-0.5MPa的加壓測試,觀察30分鐘內壓力降幅是否超過標準值(通常≤5%)。重點檢查泵蓋接合面、軸封部位是否存在滲漏,使用真空泵法檢測吸油管路真空度是否符合要求。
2. 轉速-流量特性測試
在專用試驗臺上模擬發動機工作狀態,檢測不同轉速(800-6000rpm)下機油泵的輸出流量。使用電磁流量計測量實際流量,比對理論值偏差是否超過±8%。特別關注低速啟泵能力和高速供油穩定性。
3. 壓力輸出穩定性檢測
安裝數字壓力傳感器連續監測系統油壓,要求主油道壓力在標準轉速下波動范圍不超過±0.05MPa。重點關注壓力調節閥的響應時間和溢流壓力設定值,使用示波器記錄壓力波動曲線分析異常脈動。
4. 齒輪/轉子磨損檢測
采用三坐標測量儀檢測齒輪嚙合間隙(標準值0.08-0.15mm),使用電子顯微鏡觀察齒面磨損形貌。對于轉子泵,需測量內外轉子間隙并檢查端面平面度(誤差≤0.01mm)。磨損量超過原始尺寸10%即需更換。
5. 安全閥性能驗證
測試安全閥開啟壓力是否符合設定值(通常高于工作壓力15%-20%),重復試驗3次驗證啟閉穩定性。檢測閥芯運動軌跡是否卡滯,使用表面粗糙度儀檢測閥座密封面Ra值是否≤0.4μm。
6. 油液污染度分析
采集泵腔內殘留油樣進行光譜分析,檢測金屬磨粒成分判斷磨損部位。使用顆粒計數器評估污染等級,NAS等級應控制在8級以內。金屬含量異常升高往往預示齒輪或軸承的早期失效。
7. 安裝配合間隙測量
使用塞規檢測泵體與發動機機體的安裝平面間隙(≤0.05mm),測量傳動齒輪嚙合側隙(0.10-0.15mm)。檢查聯軸器同軸度偏差(≤0.1mm),確保動力傳遞系統匹配精度。
綜合性能臺架試驗
最后需進行連續72小時的耐久試驗,模擬交替工況(冷啟動-高溫-沖擊負荷)驗證綜合性能。監測流量衰減率(應<3%)、振動值(≤4.5mm/s)和異響情況,確保所有參數滿足SAE J1516標準要求。

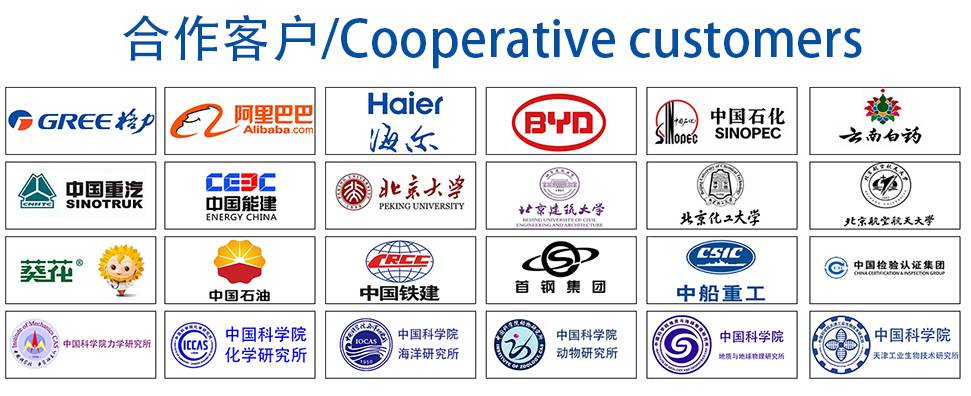