汽車電子用無源元件檢測的重要性
隨著汽車電子化、智能化的快速發展,無源元件(如電阻、電容、電感等)在車載系統中的應用場景日益增多。從發動機控制單元(ECU)、ADAS高級駕駛輔助系統到車載信息娛樂設備,無源元件在確保信號傳輸穩定、電源管理可靠等方面發揮著關鍵作用。然而,由于汽車電子需長期處于高溫、振動、濕度等復雜工況環境下,元件的性能穩定性直接關系到整車安全性和使用壽命。因此,針對汽車電子用無源元件的檢測項目需覆蓋電氣特性、環境可靠性、機械強度等多個維度,并嚴格遵循AEC-Q200、ISO 16750等行業標準,以確保元件滿足汽車級嚴苛要求。
核心檢測項目及技術要點
1. 電氣性能測試
電氣參數是無源元件功能實現的基礎檢測項目,包括:
- **電阻類**:阻值精度(±1%以內)、溫度系數(TCR)、耐脈沖電流能力;
- **電容類**:容值偏差、等效串聯電阻(ESR)、介質損耗角(DF)、耐壓特性;
- **電感類**:感量精度、Q值(品質因數)、直流電阻(DCR)等。
測試設備需采用高精度LCR測試儀,并模擬實際工作電壓和頻率范圍進行動態驗證。
2. 環境可靠性測試
針對汽車極端工況設計的多項加速老化試驗:
- **溫濕度循環**:依據ISO 16750-4標準,在-40℃~125℃范圍內進行1000次以上循環;
- **高溫存儲**:125℃下持續1000小時,驗證材料熱穩定性;
- **耐濕性測試**:85℃/85%RH環境中暴露504小時,檢測絕緣性能退化情況;
- **硫化物腐蝕試驗**:評估元件在含硫氣體環境中的抗腐蝕能力。
3. 機械強度與耐久性測試
模擬車輛振動、沖擊等物理應力:
- **機械振動**:執行20~2000Hz隨機振動測試,累計時長≥96小時;
- **機械沖擊**:半正弦波沖擊波形,峰值加速度達50G;
- **彎曲應力測試**:針對PCB組裝后的元件焊點進行疲勞強度評估;
- **端子強度測試**:通過拉力計測量引線抗拉強度(≥5N)。
4. 失效分析與材料驗證
結合破壞性/非破壞性手段進行深層質量追溯:
- **X射線檢測(X-ray)**:觀察內部結構分層、空洞等缺陷;
- **掃描電鏡(SEM)**:分析電極材料微觀形貌及失效機理;
- **成分分析**:通過EDS能譜儀驗證材料是否符合RoHS/無鉛要求;
- **熱阻測試**:評估元件散熱性能與熱匹配特性。
檢測標準與供應鏈管理
汽車電子無源元件檢測需嚴格遵循AEC-Q200可靠性認證標準,同時結合主機廠特定技術規范(如大眾VW80300、通用GMW3172)。供應鏈管理中,除批次抽檢外,還需建立從原材料溯源到生產制程的關鍵參數監控體系,并借助大數據分析預測潛在失效風險。通過全生命周期質量管理,確保元件在15年/30萬公里的汽車使用周期內保持高可靠性。

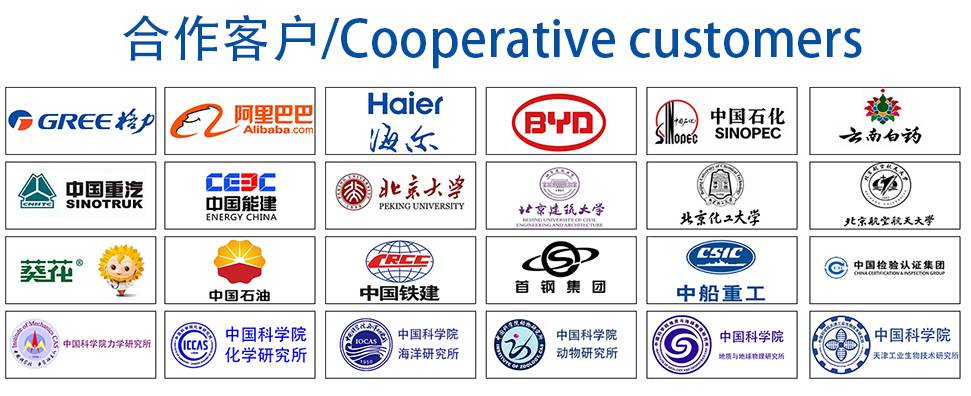