鋼制管道熔結環氧粉末內防腐層檢測項目解析
鋼制管道作為工業輸送系統中的重要載體,廣泛應用于石油、天然氣、化工等領域。為應對腐蝕介質的侵蝕,熔結環氧粉末(Fusion Bonded Epoxy, FBE)內防腐層憑借其優異的附著力、耐化學性和機械性能,成為管道內壁防護的主流技術。然而,防腐層質量直接影響管道使用壽命和安全性,需通過系統化檢測項目驗證其性能。本文圍繞鋼制管道FBE內防腐層的關鍵檢測指標展開詳細分析,為工程驗收和質量控制提供參考。
1. 外觀檢查
通過目視或內窺鏡對防腐層表面進行觀察,檢測是否存在氣泡、裂紋、剝落、雜質夾雜等缺陷。需確保涂層均勻連續,無漏涂區域。根據ISO 21809-2標準,缺陷面積占比需小于5%,且單個缺陷最大直徑不超過30mm。
2. 厚度測量
采用磁性測厚儀或超聲波測厚儀對涂層厚度進行多點抽樣檢測。根據GB/T 18593規定,FBE內防腐層標準厚度范圍為300-1000μm,允許局部最小厚度不低于設計值的80%。測量時需避開焊縫、彎頭等特殊區域,確保數據代表性。
3. 附著力測試
通過劃格法(ASTM D3359)或拉力試驗法評估涂層與基材的結合強度。標準要求劃格法測試中涂層脫落面積≤15%,拉力試驗中附著力應≥10MPa。附著力不足會導致涂層在運輸或服役過程中剝離失效。
4. 孔隙率檢測
使用高壓電火花檢測儀(電壓5-30kV)掃描涂層表面,通過電火花擊穿現象識別微孔缺陷。根據NACE RP0394標準,測試電壓按涂層厚度每100μm施加2kV計算,漏點數需≤3個/㎡。
5. 彎曲性能測試
通過冷彎試驗(ASTM D522)驗證涂層的柔韌性。將涂覆試樣在標準直徑彎芯上彎曲180°,要求涂層無裂紋或剝離。高寒地區管道需額外進行低溫(-30℃)彎曲測試。
6. 耐化學性檢測
將試樣浸入模擬介質(如10%HCl、5%NaOH溶液)中,持續30天后觀察涂層變化。要求質量損失率≤5mg/cm2,無鼓泡或軟化現象。海洋環境應用還需增加鹽水噴霧試驗(ASTM B117)。
7. 綜合性能評價
結合陰極剝離試驗(NACE TM0174)、抗沖擊試驗(ASTM G14)等,全面評估防腐層的長期服役性能。測試后剝離半徑應≤8mm,抗沖擊強度≥5J/mm。
通過上述系統化檢測項目,可有效控制FBE內防腐層質量,保障管道在復雜工況下的長期安全運行。檢測數據需與ISO 9001質量管理體系結合,建立全生命周期防腐層性能檔案。

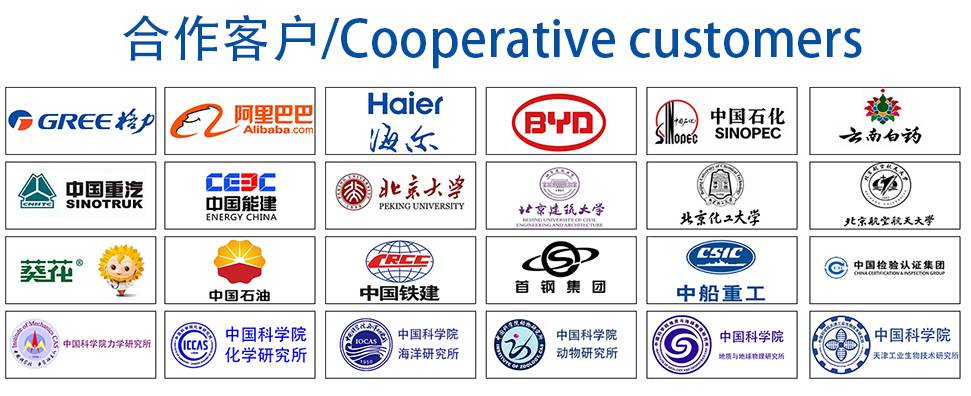