金屬材料彎曲檢測
引言
金屬材料在現(xiàn)代工業(yè)中扮演著至關重要的角色,從航空航天到汽車制造,金屬幾乎無處不在。為了確保其在不同應用中具備最佳性能,金屬材料的各項性能檢測一向是材料科學領域的重要研究課題。其中,彎曲檢測作為最為基礎卻至關重要的測試手段之一,幫助科學家和工程師評估材料的韌性、強度和塑性等關鍵特性。
金屬材料彎曲檢測的意義
彎曲檢測是材料試驗的一種常用方法,通過施加載荷使樣品工件彎曲,測試材料在受力條件下的承受能力和變形特性。與拉伸、壓縮等其他基本機械性能測試相比,彎曲測試能夠更直接模擬材料在實際使用中可能面臨的彎曲應力,從而更為準確地預估材料的使用壽命和安全性。
在金屬材料應用的實際場景中,如結構件和零部件往往會經(jīng)歷復雜的彎曲載荷。這種情況下,彎曲檢測能夠幫助我們了解金屬材料如何在彎曲應力下發(fā)生變形以至斷裂,對開發(fā)新材料和改進產(chǎn)品設計具有不可替代的指導作用。
彎曲檢測的方法與分類
金屬材料彎曲檢測通常包括三點彎曲試驗和四點彎曲試驗兩大類。三點彎曲試驗是指在樣品中部施加加載點,并使兩端支撐在固定位置。它可以快速且高效地提供材料的彎曲強度及剛度信息。而四點彎曲試驗則在樣品兩側(cè)分別施加一對加載點,相對三點測試更為復雜,但對材料在多點受力下的響應評估更加準確。
彎曲試驗中,測試設備通常包括萬能測試機、彎曲夾具和相應的數(shù)據(jù)采集系統(tǒng)。隨著科技的進步,非接觸式測量技術,如光學跟蹤和影像分析等也逐漸被運用到彎曲檢測中,以提高數(shù)據(jù)精度和測試效率。
彎曲檢測的主要參數(shù)與結果分析
在彎曲檢測中,研究人員重點關注幾個關鍵參數(shù):彎曲模量、屈服強度、極限彎曲強度和塑性形變能力等。彎曲模量表明材料對彎曲應力的抵抗能力,屈服強度則是材料開始發(fā)生塑性變形的位置,極限彎曲強度是材料在彎曲過程中能承受的最大應力,塑性形變能力則展示了材料在承受彎曲應力后不發(fā)生斷裂而持續(xù)變形的特性。
通過對這些參數(shù)的深入分析,我們可以推斷出材料在各種條件下的使用性能。例如,在汽車制造中,經(jīng)過彎曲檢測后能夠幫助工程師選擇具有最佳彎曲強度和韌性的鋼材用于車身結構和安全組件,從而提高車體的整體安全性能。
影響彎曲檢測結果的因素
影響彎曲檢測結果的因素有很多,其中包括測試樣品的幾何形狀、材料狀態(tài)、測試速度、環(huán)境溫度和設備校準等。測試樣品的尺寸和形狀對于檢測結果尤為重要,特別是厚度和橫截面積的變化會直接影響彎曲強度的計算。
材料的初始狀態(tài)(如冷軋、熱軋或退火處理)同樣會顯著影響測試結果。測試速度的變化也可能導致結果的差異,因為加載速率可能影響材料內(nèi)部的應力分布和熱效應。此外,隨著溫度變化材料性能的不同響應也將影響測試結果,因此檢測環(huán)境的溫度控制非常重要。
彎曲檢測在實際工業(yè)中的應用案例
具體應用中,彎曲檢測被廣泛用于監(jiān)控生產(chǎn)工藝的穩(wěn)定性和產(chǎn)品的質(zhì)量控制。例如,在建筑鋼材的生產(chǎn)中,彎曲檢測可以幫助確保鋼筋達到所需的抗彎性能,進而保證建筑結構的穩(wěn)定。航空航天工業(yè)中,鈦合金和鋁合金的彎曲測試確保機體結構在極端條件下不會發(fā)生過早失效。
同時,在家電行業(yè),金屬薄板的彎曲性能直接影響產(chǎn)品外殼的耐用性與安全性。定期的彎曲檢測有助于廠家快速發(fā)現(xiàn)潛在的產(chǎn)品缺陷并進行整改,從而提升產(chǎn)品質(zhì)量和用戶滿意度。
未來的發(fā)展趨勢與挑戰(zhàn)
隨著金屬材料應用領域的不斷擴大和產(chǎn)品需求的個性化發(fā)展,彎曲檢測技術也在不斷進步。未來,自動化和智能化檢測將成為趨勢,不僅能夠進一步提高檢測精度,還可實現(xiàn)大規(guī)模生產(chǎn)線的實時監(jiān)控。此外,材料仿真和計算機模擬正成為彎曲檢測的重要補充手段,為材料的預測性能提供可靠預測。
然而,隨著不斷發(fā)展的材料科學,新的挑戰(zhàn)也隨之而來。復合材料和合金的多樣性和復雜性使得傳統(tǒng)彎曲檢測方法面臨設計與實施的困難。在這種背景下,開發(fā)適用于新材料的彎曲檢測技術,并將其與齊全的微觀結構分析結合,將是未來的重要研究方向。
結論
總之,金屬材料的彎曲檢測在現(xiàn)代工業(yè)生產(chǎn)中具有重要意義。通過對金屬材料在彎曲應力下的性能監(jiān)測和分析,可以有效地提高產(chǎn)品的安全性和可靠性,推動未來科技的發(fā)展。盡管面對復雜材料體系所帶來的挑戰(zhàn),持續(xù)的技術創(chuàng)新和跨學科合作將確保彎曲檢測方法的不斷完善與廣泛應用。

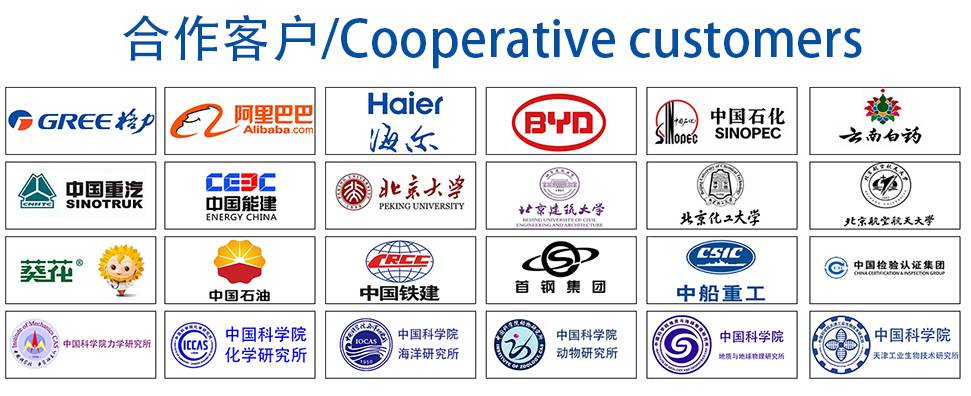